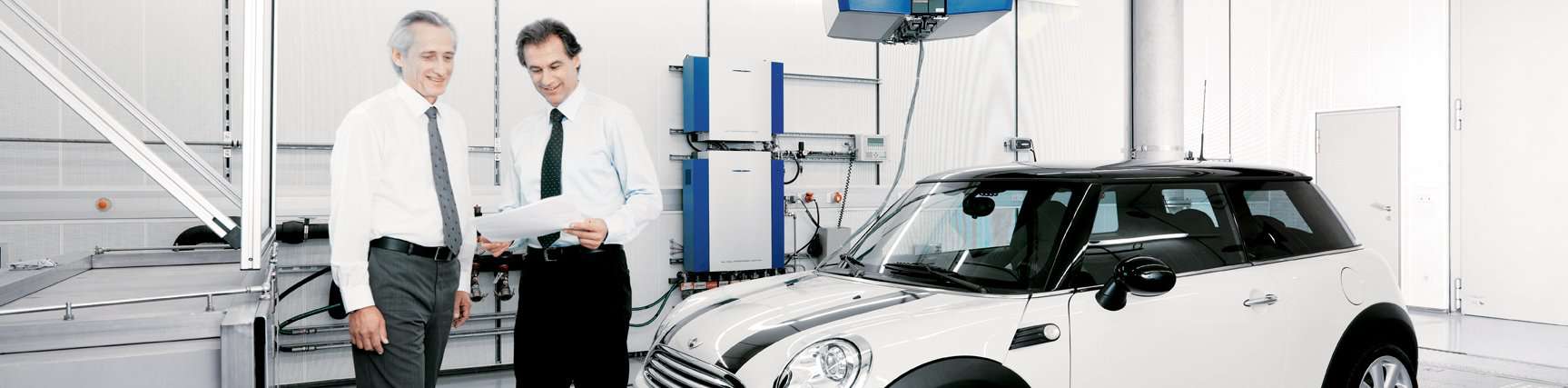
AVL List
AVL has maximum quality requirements. This also applies to customer services. The previously used field service management software had serious performance and usability issues in the mobile solution. In 2009 this led to the decision to replace the existing software by the products of mobileX. By using standardized processes and the solutions of mobileX, AVL was able to increase the service quality to a great extent within the scope of the strategic project AVL-FSM (field service management).
Using the field service management software mobileX-Dispatch the dispatcher can plan service calls across different time zones. The feature „global resource search“ shows the dispatcher service technicians on a global level, which are available and have the necessary skills for a certain order.Apart from Germany and Austria the solution is already in use in with AVL North America, South America, Italy, France, UK, Nordiska, Iberica, India, Japan, South Korea and ASEAN.
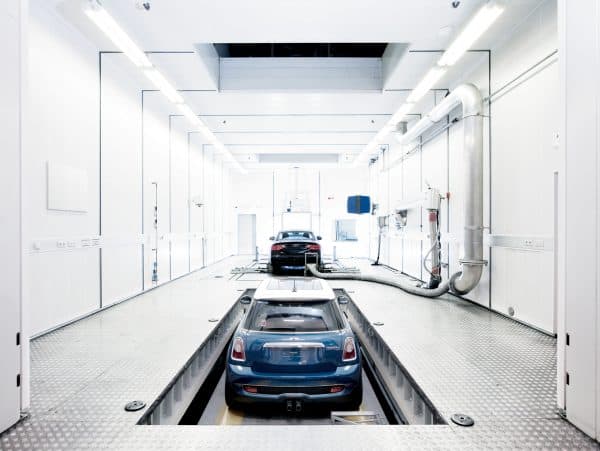
Using the mobile solution mobileX-MIP for Field Service the service technician gets access to all relevant information from SAP related to the order as well as to the service history of the respective machine. The technician can create the necessary service reports and have them signed by the customer on a digital sign-pad. The productive and non-productive hours as well as absences are transferred to SAP CATS, the central time reporting system. On top of that the service technician can use SAP material via mobileX-MIP. In case of a SAP equipment (serialized material) an equipment assembly or disassembly can be carried out. Thus information in SAP about the AVL Installed Base can be kept up-to-date with little effort.
At AVL service calls for maintenance and fault clearances are usually short-term and take between one and five days. Installations on the other hand often take several months. Especially for longer lasting service calls mobileX-MIP for Field Service offers the opportunity to create any number of performance records for an order. Due to this the headquarters is always on the run about the progress of the order and is able to bill intermediate invoices.
By collecting internal quality reports consistently in SAP the central quality department in Graz can now give even more easily a sophisticated feedback to product development. This is especially relevant for faulty parts in warranty.
Conclusion
By introducing mobileX‘s mobile solution and field service management solution AVL could improve the efficiency and quality in the customer services department drastically and decrease costs at the same time. The time zone support of the solutions allows AVL to act globally. When choosing the new mobile system the decisive factors for AVL were usability, performance as well as the integration into SAP. With mobileX the company was very optimistic to solve the existing issues and media disruptions in the medium term. Already after a short time the dispatchers and technicians were able to work with the new solutions independently.

Using mobileX-Dispatch and mobileX-MIP for Field Service we can ensure a high service quality and contribute to continiously improve the AVL products. Media disruptions between field service technicians and back office colleagues can be minimized. Affiliates report fewer sources of error as well as less administrative work. They also can issue invoices quicker. This has also resulted in the fact that the investments in our affiliates pay off after about 18 months due to the savings.
AVL Electrification

AVL List is the world’s largest privately owned company for development, simulation, and testing technology for powertrains on passenger cars, lorries and large engines. The Austrian company is a supplier for many globally leading automakers such as Mercedes Benz, BMW, Hyundai, and many others.In 2012, the company posted revenue of around €1 billion and had 6,200 employees worldwide.